Textile printing has a rich and varied history, evolving from ancient methods to the cutting-edge technologies we see today. This journey through time reveals the ingenuity and creativity that have shaped the fabric printing industry, reflecting cultural shifts and technological advancements. In this blog, we will explore the evolution of textile printing techniques, highlighting significant milestones and innovations that have transformed the way we create and use printed fabrics.
Ancient Textile Printing Techniques
The origins of textile printing can be traced back to ancient civilizations, where artisans developed ingenious methods to embellish fabrics with intricate designs.
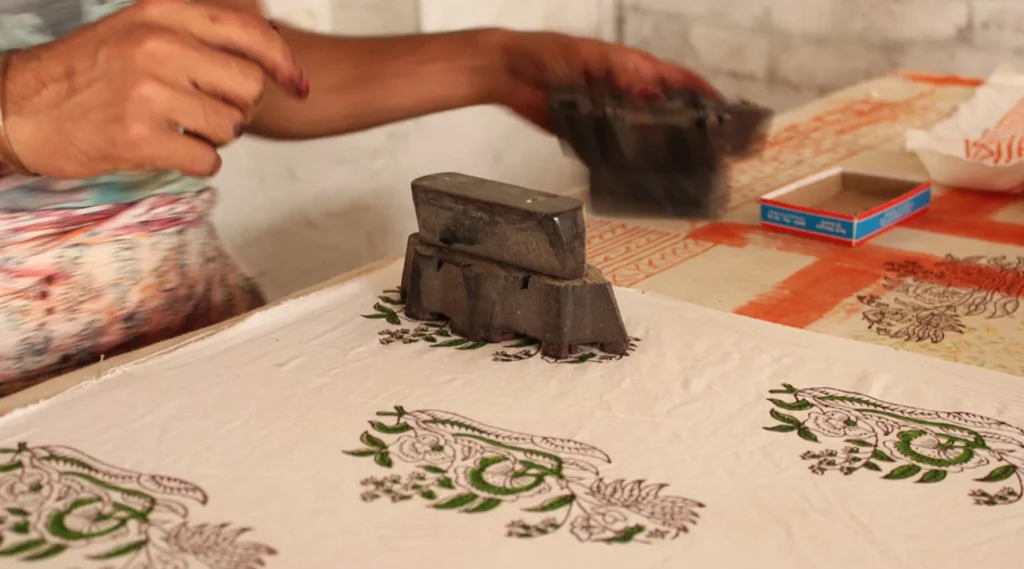
- Block Printing
Block printing is one of the oldest forms of textile printing, dating back to around 3000 BCE in Egypt and later in China and India. Artisans carved designs onto wooden blocks, applied dye to the block’s surface, and then pressed it onto the fabric. This technique allowed for repeated patterns and intricate details, making it popular for decorative textiles. - Tie-Dye and Resist Dyeing
Tie-dyeing and resist dyeing techniques have ancient roots in various cultures, including Africa, Asia, and South America. These methods involved tying, folding, or using wax to resist dye on certain parts of the fabric, creating unique patterns and vibrant colors.
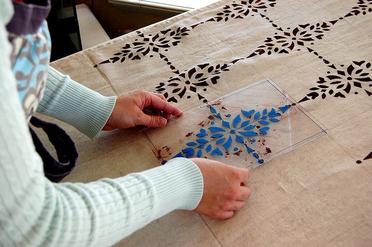
Medieval and Renaissance Advancements
During the medieval and Renaissance periods, textile printing techniques saw significant developments, particularly in Europe and Asia.
- Stencil Printing
Stencil printing emerged as a popular technique in Japan during the Heian period (794-1185 CE). Artisans used paper or metal stencils to apply dye to fabric, creating detailed and repetitive patterns. This method influenced European printing practices in the later centuries. - Copperplate Printing
In the 17th century, copperplate printing revolutionized textile printing in Europe. Artisans engraved intricate designs onto copper plates, which were then used to transfer the designs onto fabric. This technique allowed for greater detail and precision, making it ideal for producing elaborate patterns on fine fabrics.
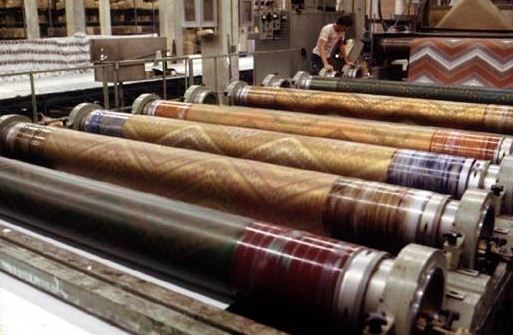
The Industrial Revolution
The Industrial Revolution brought about a significant transformation in textile printing, with the advent of mechanization and mass production.
- Roller Printing
Invented in the late 18th century, roller printing involved engraving designs onto cylindrical rollers. As the fabric passed through the rollers, the design was printed continuously, allowing for high-speed production and consistent patterns. This technique greatly increased the efficiency and accessibility of printed fabrics. - Screen Printing
Screen printing, which originated in China during the Song Dynasty (960-1279 CE), gained popularity in the Western world during the 20th century. This method uses a mesh screen to transfer ink onto fabric, with each color requiring a separate screen. Screen printing is versatile and widely used for both artistic and commercial applications. To learn more about this method, visit our blog on All about Screen Printing.
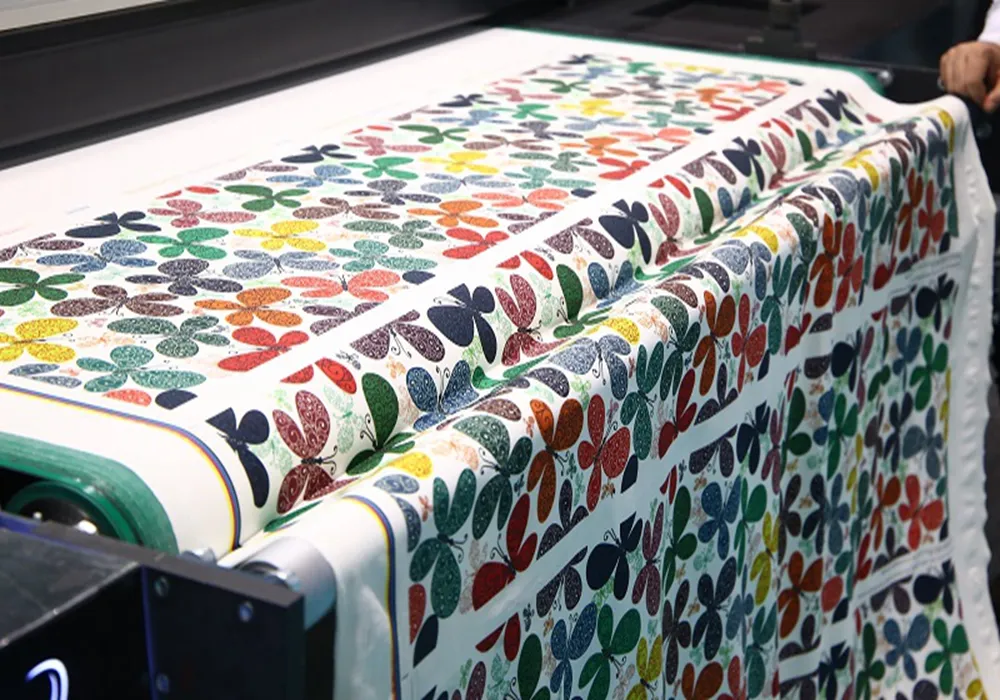
Modern Innovations in Textile Printing
The 21st century has seen remarkable advancements in textile printing technologies, driven by digital innovations and a focus on sustainability.
- Digital Printing
Digital printing technology allows for the direct application of designs onto fabric using inkjet printers. This method offers unparalleled precision and flexibility, enabling the production of complex, multi-colored patterns without the need for screens or plates. Digital printing is ideal for custom and small-batch production, reducing waste and environmental impact. - Sublimation Printing
Sublimation printing involves transferring dye onto fabric using heat and pressure. This technique is particularly effective for synthetic fabrics like polyester, producing vibrant, long-lasting colors. Sublimation printing is widely used in sportswear, home textiles, and personalized products. - Eco-Friendly Printing Technologies
As environmental concerns grow, the textile industry is embracing eco-friendly printing technologies. Water-based inks, organic dyes, and sustainable production methods are becoming standard practices, reducing the ecological footprint of textile printing. For insights into the latest innovations, check out our blog on Innovations in Fabric Printing: Breaking the Boundaries of Traditional Methods.
The Future of Textile Printing
The future of textile printing lies in continuous innovation and sustainability. Emerging technologies like 3D printing and smart textiles are set to revolutionize the industry, offering new possibilities for creativity and functionality. These advancements will further enhance the efficiency, quality, and environmental sustainability of textile printing.
Conclusion
The evolution of textile printing techniques from ancient to modern times is a testament to human ingenuity and creativity. From the earliest block printing methods to the latest digital technologies, each advancement has contributed to the rich tapestry of textile design and production. Understanding this history not only highlights the progress made but also inspires future innovations in the field.
For comprehensive printing services and high-quality textiles, visit locofast.com. Locofast offers a wide range of fabric printing solutions, leveraging the latest technologies to meet your needs. Explore their website to learn more about their services and how they can help you stay ahead in the textile industry. For a detailed overview of the offerings, visit our blog on Printing services by Locofast.