The Origins of Textile Printing
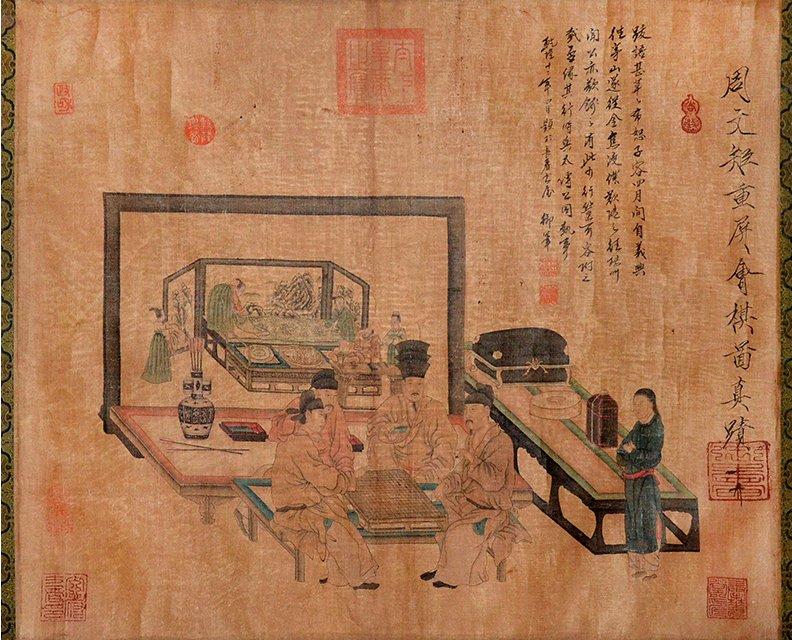
The history of textile printing can be traced back to ancient civilizations, including Egypt, China, and India. These cultures utilised different methods to apply colours and designs to fabrics, often employing techniques such as block printing and resist dyeing. In block printing, wooden blocks engraved with intricate patterns were dipped in coloured dyes and pressed onto the fabric, creating visually striking designs. Resist dyeing involved applying wax or other substances to the fabric to prevent the absorption of dye, resulting in mesmerising patterns and colour contrasts.
Introduction to Screen Printing
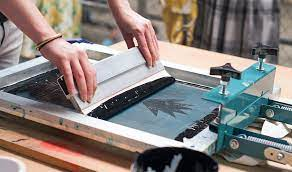
Screen printing, also known as silkscreen printing in its traditional form, emerged as a revolutionary technique in the world of textile printing. The process involves using a mesh screen, typically made of polyester or stainless steel, to transfer ink onto fabric. A stencil is used to block certain areas on the mesh, rendering them impermeable to the ink. When ink is applied and the screen is lifted away, the ink remains on the fabric, creating the desired design.
The Role of Mesh in Screen Printing
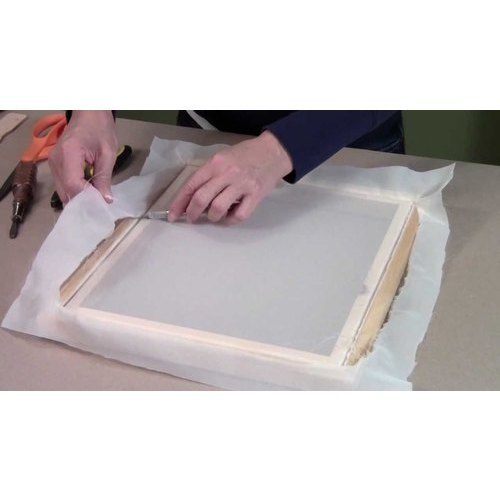
The mesh plays a crucial role in screen printing, and its proper tension is essential for accurate colour registration and print quality. Finer mesh, with a higher number of threads per inch (200-260 threads per inch), is ideal for graphic and industrial printing, as it allows for intricate and precise designs. On the other hand, coarser mesh, with fewer threads per inch (160-180 threads per inch), facilitates more ink application, making it suitable for bold and vibrant designs.
The Intricacies of Textile Printing Chemicals
Textile printing involves a diverse array of dyes and pigments, each offering unique properties and characteristics. Vat, reactive, naphthol, and disperse colours are some of the commonly used dyes, renowned for their excellent fastness properties and ability to bond effectively with various types of fibres. Additionally, pigments, although not true dyes, are widely used in printing. They are fixed to the fabric through resins that provide exceptional resistance to laundering or dry cleaning. Pigments are favoured for their longevity and are particularly effective for achieving light to medium shades.
The choice of dyes depends on the type of fibre being printed on. For instance, cotton is often printed with vat and reactive dyes, while silk is best suited for acid colours. Wool, another popular fabric in textile printing, is printed with acid or chrome dyes, but not before undergoing a chlorine treatment to enhance its receptivity to colours. Man-made fibres, such as polyester and nylon, are generally printed with disperse and cationic dyes, which ensure vibrant and long-lasting results.
Types of Screen Printing: A Tale of Rotary and Flat Screen Techniques
Screen printing has evolved into two primary types based on the kind of screen used: Rotary Screen Printing and Flat (Bed) Screen Printing.
a) Rotary Screen Printing:

This method employs a cylindrical screen that rotates in a fixed position, allowing for continuous fabric printing at high speeds. Rotary presses place the squeegee within the screen, allowing for efficient and consistent ink transfer. This type of screen printing has become the most common technology today, enabling the production of intricate designs and multicoloured images with ease. With typical speeds ranging from 50 to 120 yards per minute, rotary screen printing has revolutionised the textile printing industry.
b) Flat (Bed) Screen Printing:
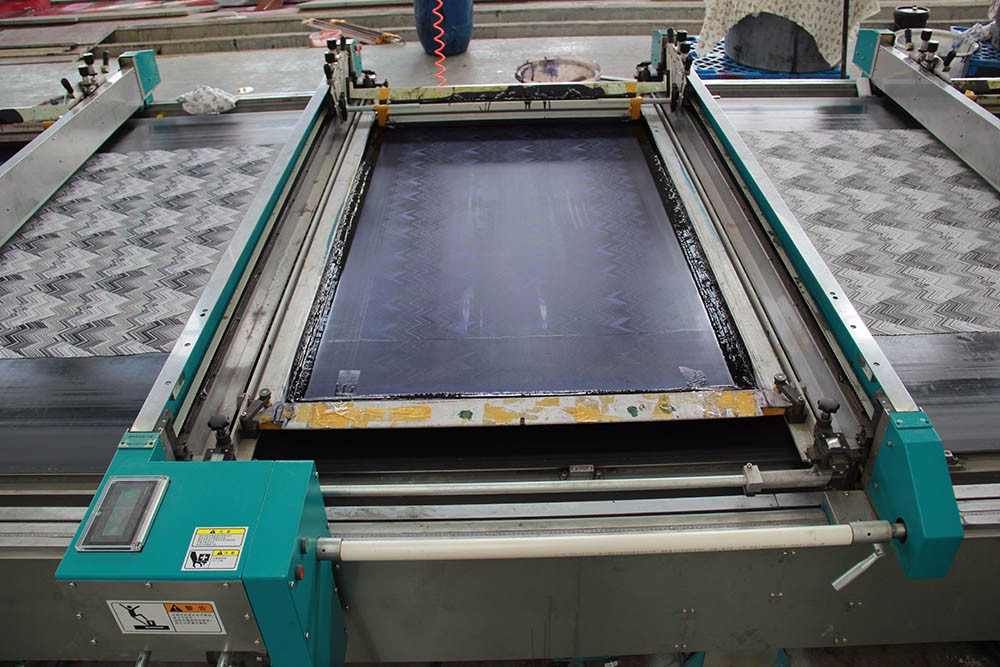
In this automated version of the hand-operated silk screen printing, separate screens are constructed or engraved for each colour in the print design. Although it operates on a semi-continuous start-stop basis, flat screen printing still holds its place in the industry. It finds particular application in printing terry towels and contributes to around 15-18% of the global printed fabric production.
Conclusion: Embracing the Beauty of Textile Printing
The art of textile printing, through screen printing and its variants, allows for the creation of intricate and stunning designs on fabrics. The interplay of mesh, chemicals, and printing technique holds the key to unlocking the full potential of this captivating art form. Whether you’re admiring a vibrant pattern on your favourite garment or marvelling at the creativity of textile artists, understanding the techniques behind textile printing adds a new layer of appreciation to the world of fabrics.
As we embrace the heritage and innovation of textile printing, we recognize the indelible mark it has left on the fabrics that surround us. From the intricacies of ancient resist dyeing to the modern speed and precision of rotary screen printing, textile printing continues to captivate our senses and elevate the beauty of everyday fabrics. So, the next time you don a printed garment or admire an exquisite textile design, take a moment to appreciate the artistry and craftsmanship that went into transforming a simple piece of fabric into a work of art.