A series of processes known as yarn manufacturing transforms unprocessed cotton fibres into yarn that may be used in a variety of end products. The clean, robust, and uniform yarns required in modern textile markets require a number of techniques.
Fiber preparation
Fibers are transported in the form of bales and are opened manually or mechanically. Synthetic fibers merely need to be separated, however natural fibres may need cleaning. The picker breaks up and separates the fibre lumps, and if necessary, cleans the fibre as well.
For some applications, the blending of different staple fibres may be necessary. When the lap is being formed, the fiber being carded, or being drawn out, blending may take place. Each fiber’s quantity is measured meticulously, and its proportions are kept constant.
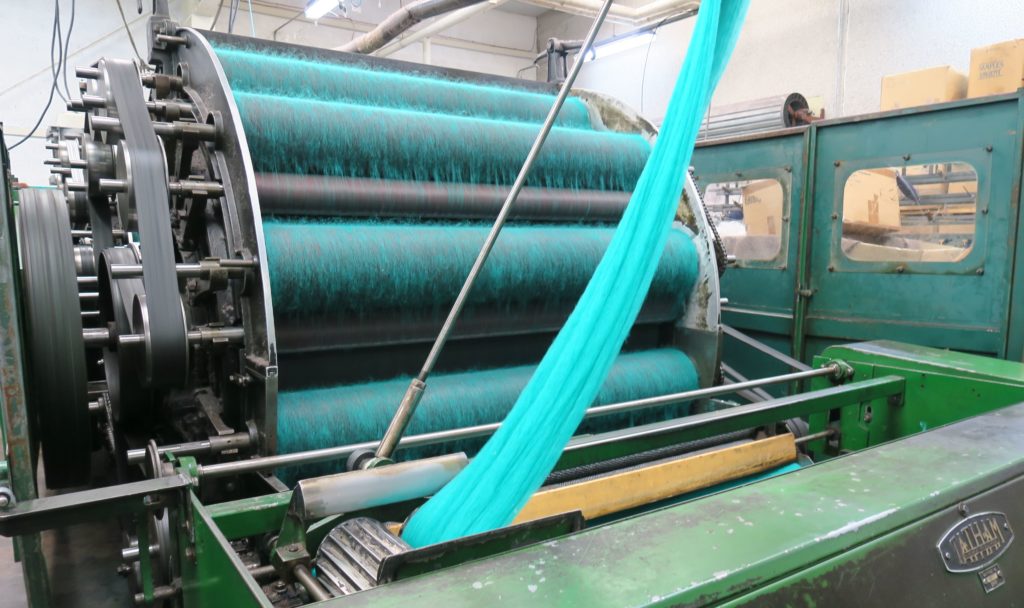
Carding
The carding machine utilizes numerous fine wires to isolate the fibers and draw them into a relatively parallel shape, creating a delicate fiber web. This web then moves through a funnel-shaped device that creates a strand of parallel fibers similar to a rope. It is possible to blend different fibers by joining laps of various fibers.
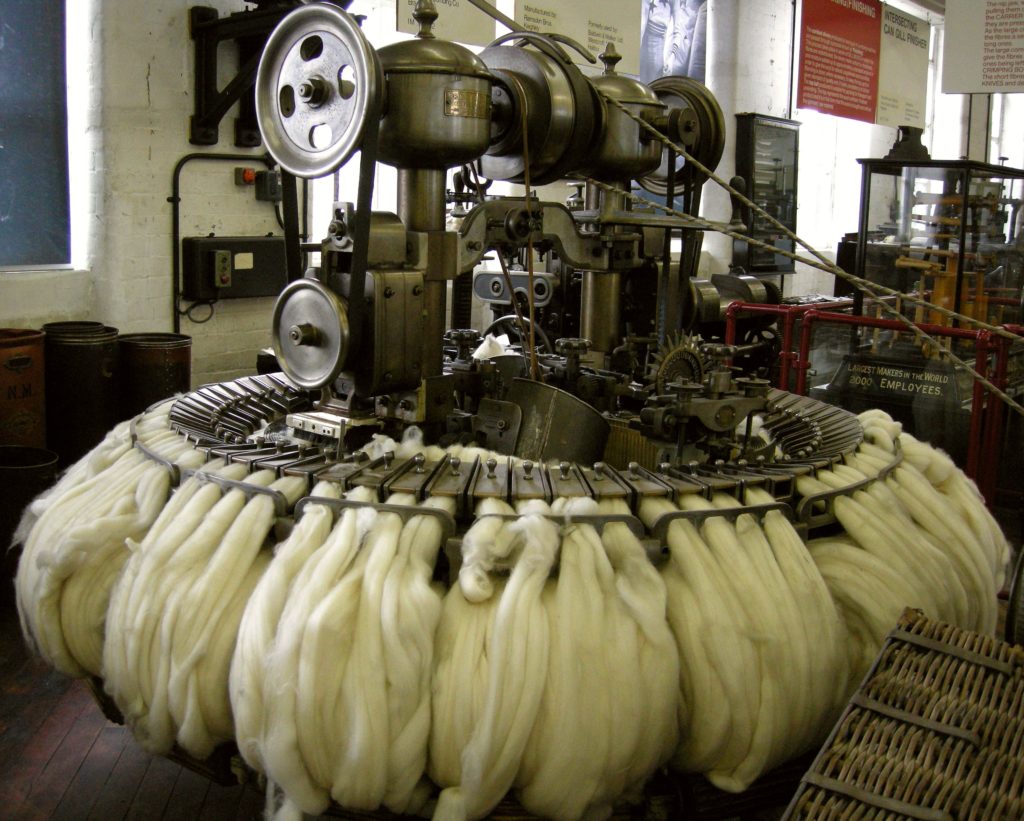
Combing
To produce a smoother and finer yarn, fibers undergo an additional method of paralleling. A device resembling a comb organizes fibers into parallel form, causing shorter fibers to be removed from the strand.
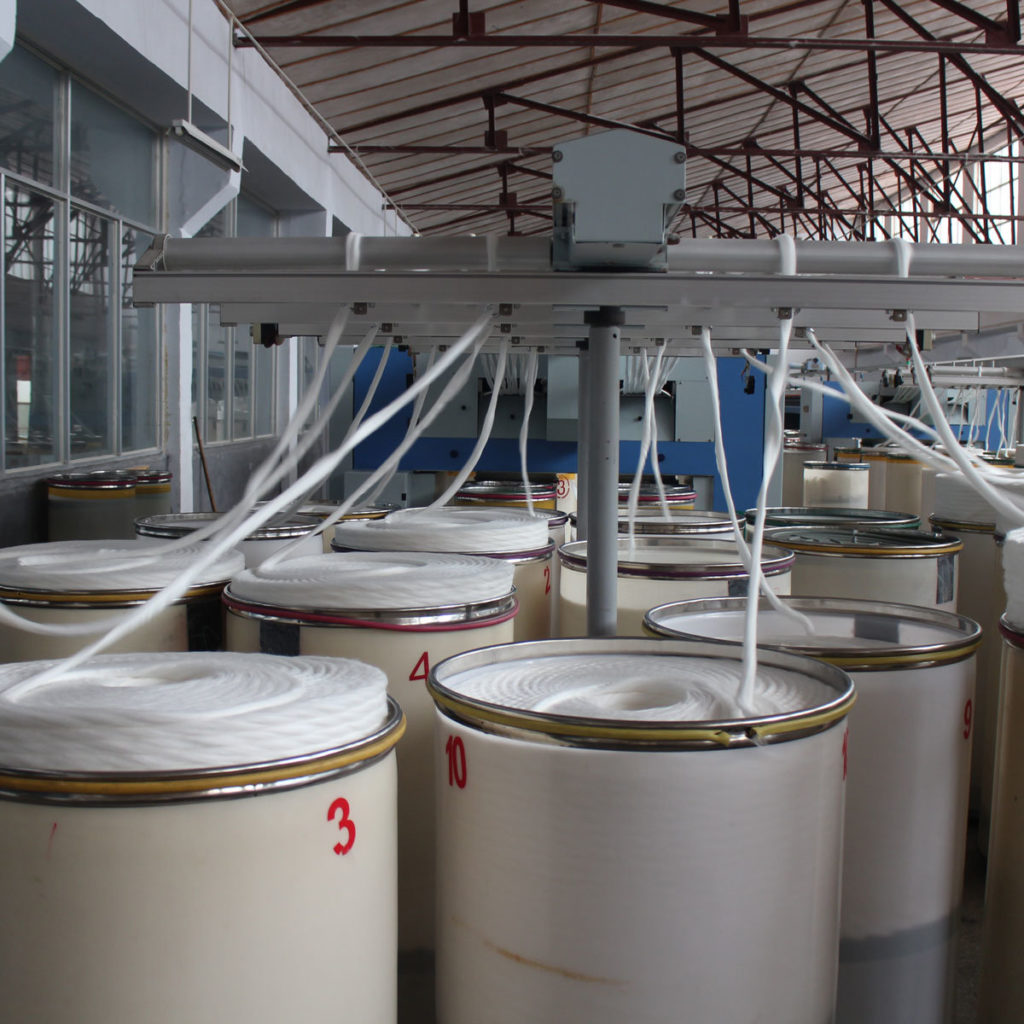
Drawing out
Once fibers have undergone carding or combing, they are referred to as sliver. Prior to this process, multiple slivers are combined. A set of rollers that rotate at varying speeds stretch out the sliver into a more consistent strand that is twisted slightly and then put into large cans. Carded slivers go through two rounds of drawing after carding, while combed slivers go through one drawing step before combing and two more drawing steps after combing.
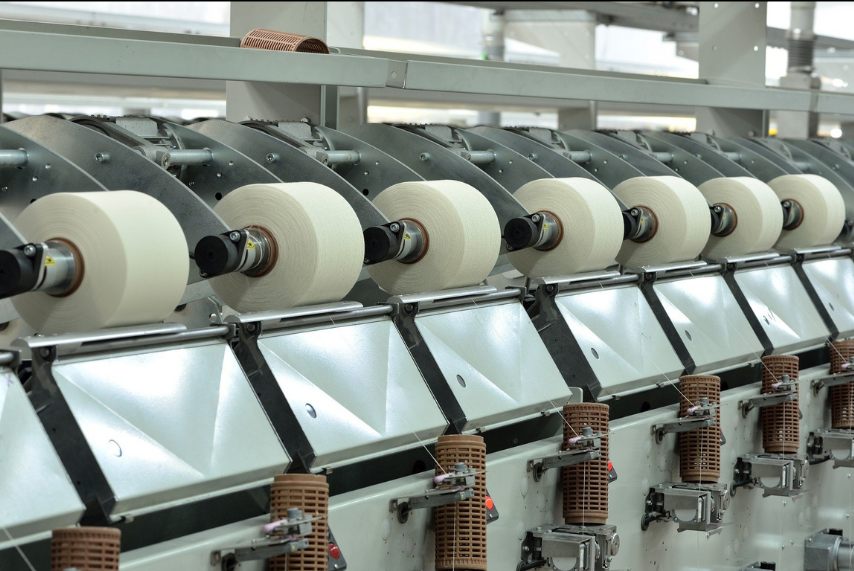
Twisting
The sliver undergoes another elongation and twisting process in the roving frame machine, resulting in the creation of elongated strands known as roving.
Spinning
Two common commercial methods for producing yarn are ring spinning and open-end spinning.
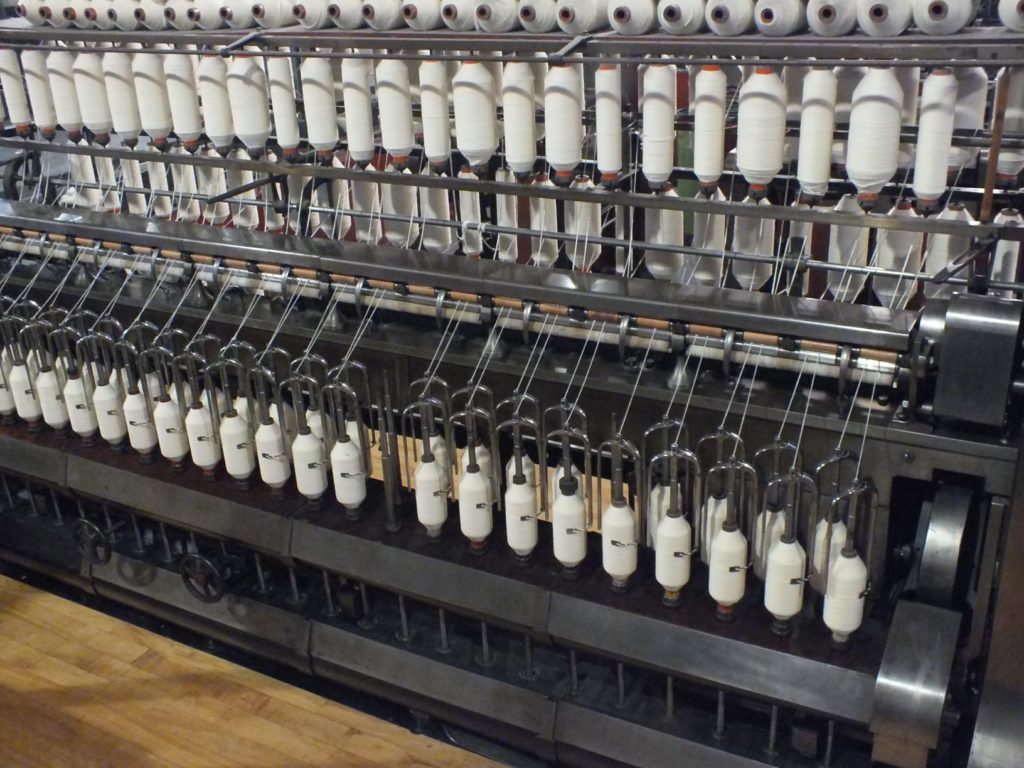
Ring spinning is a common method of yarn formation where the roving is fed through rollers and elongated before passing through the eyelet and moving down to the traveler. The traveler then moves freely around a stationary ring at high speeds, while the spindle turns the bobbin at a constant speed. This simultaneous turning and movement of the traveler creates the necessary twist and winds the yarn in one continuous operation.
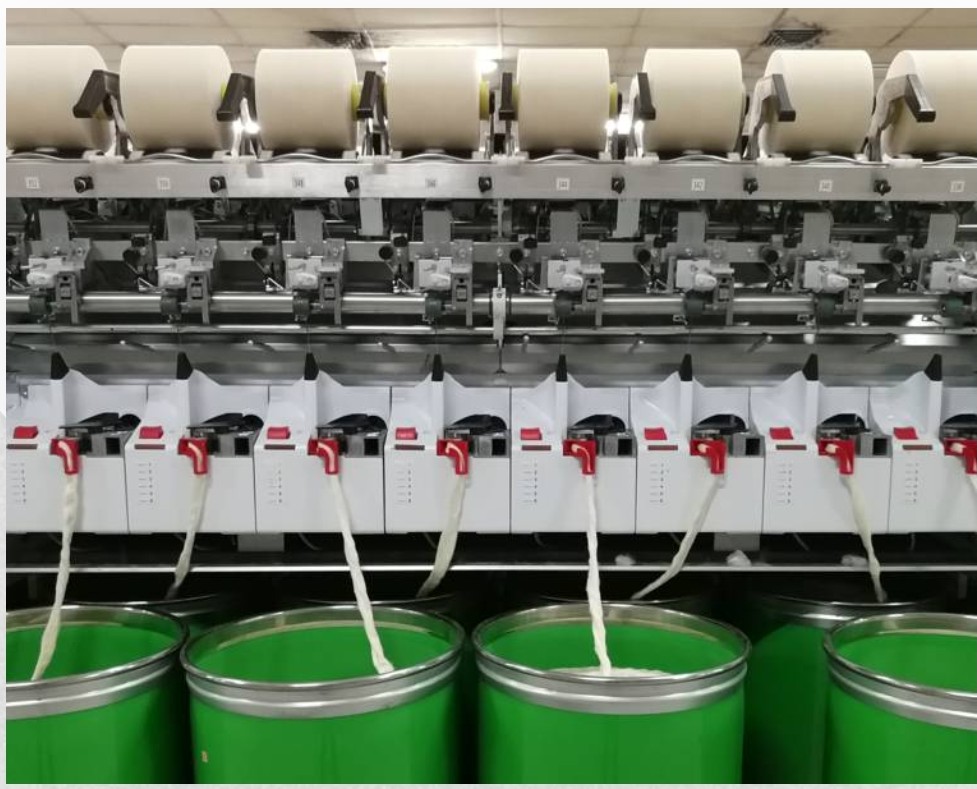
Open-end spinning does not require the use of roving. Instead, a stream of air is used to feed a sliver of fibers into the spinner. The rotary beater separates the fibers and directs them into a V-shaped groove on the rotor with the help of air current. When the rotor rotates, it produces twist. As the process continues, fresh fibers are added to the groove, and the formed yarn is collected at the end.
Quality Control
The utilization of automation has simplified the process of attaining quality in the production of yarn. With the aid of electronics, various aspects such as temperature, speed, twist, and efficiency can be controlled. In addition to this, the American Society for Testing of Materials has introduced standardized methods that enable the measurement of properties such as drawforce, bulk, and shrinkage.