In the vast landscape of textiles, non-woven fabrics stand as a testament to innovation and versatility. Unlike their woven or knitted counterparts, non-wovens are created through unique manufacturing processes that involve bonding or felting fibers together. This blog takes a deep dive into the diverse applications and intricate manufacturing techniques that make non-woven fabrics indispensable in various industries.
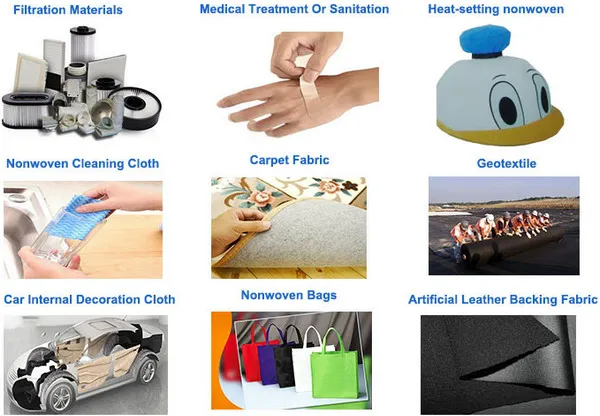
Uses of Non-Woven Fabrics
Medical Applications:
In medical settings, non-woven fabrics play a pivotal role in the creation of surgical gowns and masks. The inherent properties of sterility and breathability make them essential in maintaining a hygienic environment.
Automotive Industry:
Within the automotive industry, non-woven fabrics find applications as insulation and soundproofing materials. Their ability to provide effective insulation and dampen sound contributes to enhanced comfort in vehicles.
Construction – Geotextiles:
Non-wovens are vital in geotextiles for construction, where they provide stability and drainage capabilities. These fabrics contribute to the durability and longevity of infrastructure projects.
Everyday Essentials:
Everyday items like disposable diapers and wipes owe their absorbency and disposability to non-woven fabrics. The versatility of these fabrics extends to various aspects of daily life.
Fashion Industry:
Even in the fashion industry, non-wovens have found their place. Used for interlining, they provide structure to garments, showcasing the adaptability of these fabrics across diverse sectors.
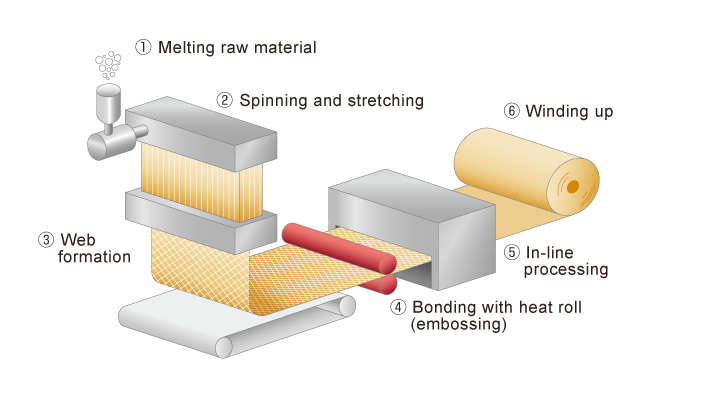
Manufacturing Processes
The manufacturing of non-woven fabrics involves several processes:
- Dry-Laid Process: Here, fibers are laid down in a web or mat form and then bonded mechanically, thermally, or chemically. This method is common for fabrics requiring high strength and dimensional stability.
- Wet-Laid Process: Similar to papermaking, this process suspends fibers in a liquid to lay them down into a web. It’s ideal for creating fabrics with a high level of uniformity and smoothness.
- Spunbond Process: Fibers are spun into fine threads and laid into a web, which is then bonded. This technique is efficient for large-scale production and results in durable fabrics.
- Melt-Blown Process: In this method, polymers are melted and blown into fine fibers, creating fabrics with good filtration properties.
Comparisons with Woven Fabrics
Unlike woven fabrics, detailed in “Understanding weaving and fabric loom types,” non-woven fabrics don’t require the conversion of fibers into yarn. This difference in manufacturing results in unique characteristics like greater flexibility in thickness and density. While woven fabrics, such as those in “Types of Cotton Blends: Unveiling the Fusion of Comfort and Innovation,” offer comfort and breathability, non-wovens provide structural integrity and specific functionalities like filtration and insulation.
Fabric Sourcing Considerations
When sourcing non-woven fabrics, understanding their specific properties and manufacturing methods is crucial. As discussed in “A guide to fabric sourcing,” selecting the right type of fabric for a specific application requires thorough knowledge of its characteristics and production processes.
Conclusion
Non-woven fabrics emerge as indispensable players in various sectors, thanks to their specialized properties and unique manufacturing methods. For businesses seeking top-notch non-woven fabrics, Locofast stands as a reliable source, offering a diverse range of options that cater to the dynamic needs of different industries. The intricate world of non-woven fabrics continues to unfold, proving its significance in shaping a wide array of applications across the textile landscape.