Digital printing has revolutionized the textile industry, offering unparalleled flexibility, efficiency, and creative freedom. This technology enables manufacturers to produce vibrant, intricate designs with minimal environmental impact and reduced production times. In this blog, we will delve into the world of digital printing in textiles, exploring its advantages, processes, and its transformative impact on the industry.
What is Digital Printing in Textiles?
Digital printing in textiles involves the application of digital technology to print designs directly onto fabric. Unlike traditional methods, which rely on screens or rollers, digital printing uses inkjet or laser printers to transfer designs from a computer onto textiles. This method allows for precise and detailed prints, making it ideal for complex patterns and vibrant colors.
The Process of Digital Printing
- Design Creation: The process begins with the creation of a digital design using graphic design software. This design can be as intricate or simple as needed, and changes can be made easily without the need for new screens or plates.
- Fabric Preparation: The fabric is pre-treated with a coating that helps the ink adhere better and ensures vibrant colors. This step is crucial for achieving high-quality prints.
- Printing: The prepared fabric is fed into the digital printer, where the design is printed directly onto the textile. The printer uses high-speed inkjet technology to apply the design with precision.
- Fixation: After printing, the fabric undergoes a fixation process, usually involving heat or steam, to set the ink and ensure durability.
- Post-Treatment: The printed fabric is then washed and dried to remove any excess ink and ensure the print’s longevity.
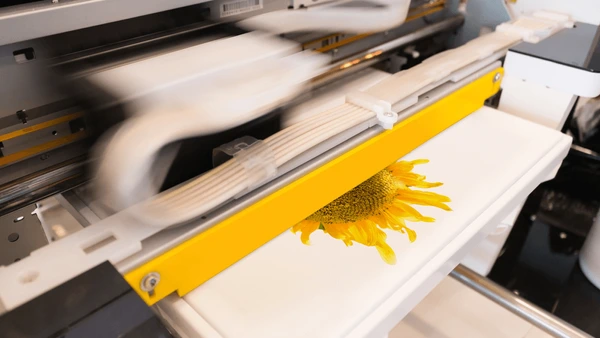
Advantages of Digital Printing in Textiles
- Design Flexibility: Digital printing allows for unlimited color combinations and intricate designs. It is easy to make modifications to designs, making it ideal for customized and limited-edition prints.
- Speed and Efficiency: Digital printing significantly reduces setup times and is faster than traditional methods. This speed is crucial for meeting tight deadlines and keeping up with fast fashion trends.
- Cost-Effective for Small Runs: Unlike traditional methods, digital printing is cost-effective for small production runs. There is no need for screens or plates, reducing setup costs.
- Environmental Benefits: Digital printing uses less water and produces less waste than traditional printing methods. It also uses eco-friendly inks, making it a more sustainable option.
For more insights on how digital technology is transforming the textile industry, read our blog on The Impact of Digital Technology on Textile Design and Production.
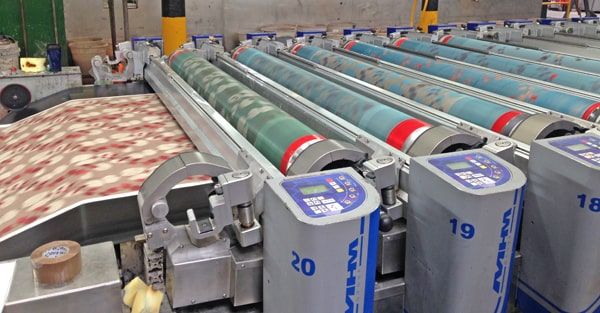
Comparing Digital Printing to Traditional Methods
- Screen Printing: Screen printing involves creating a stencil (or screen) for each color and then applying the ink through the screen onto the fabric. While it is cost-effective for large runs, it lacks the flexibility and speed of digital printing. For a detailed comparison, check out our blog All about Screen Printing.
- Rotary Printing: Rotary printing uses engraved cylinders to apply designs onto fabrics. It is suitable for high-volume production but involves significant setup costs and longer lead times compared to digital printing.
Innovations in Digital Printing
The digital printing landscape continues to evolve with innovations that push the boundaries of what is possible. Advanced ink formulations, improved printer technologies, and integration with smart textiles are just a few examples. These innovations are enabling more sustainable practices and opening up new creative possibilities. To learn more about the latest advancements, visit our blog Innovations in Fabric Printing: Breaking the Boundaries of Traditional Methods.
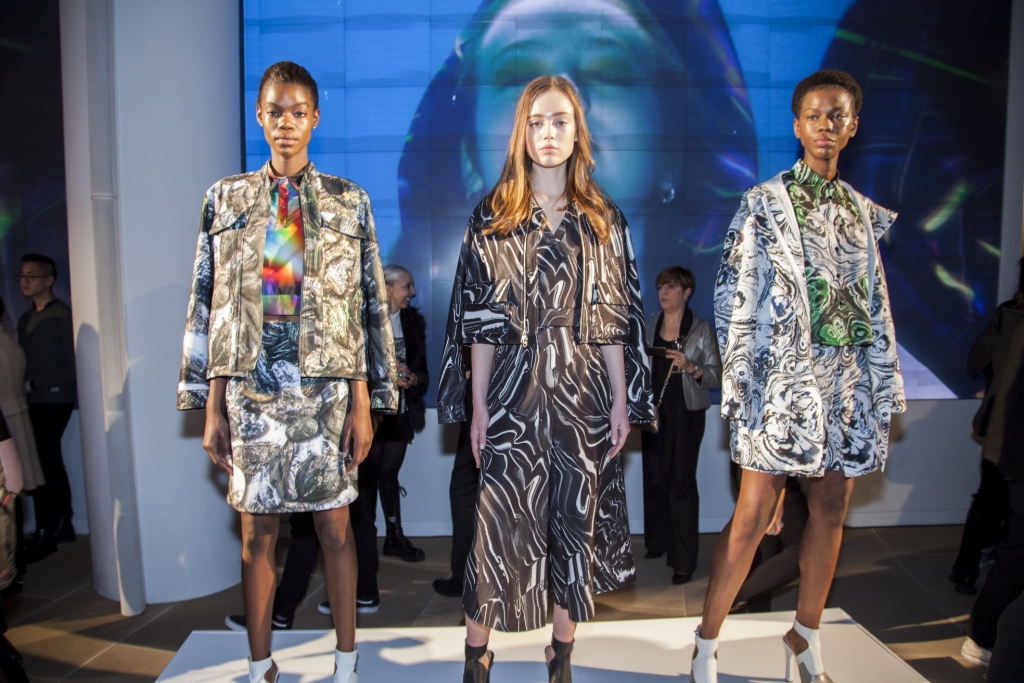
Applications of Digital Printing
Digital printing is used in various textile applications, including:
- Fashion: From haute couture to fast fashion, digital printing allows designers to experiment with colors, patterns, and textures without the constraints of traditional methods.
- Home Textiles: Digital printing is ideal for producing customized home textiles such as curtains, cushions, and bed linens.
- Sportswear: The ability to produce detailed and durable prints makes digital printing perfect for sportswear, where performance and aesthetics go hand in hand.
Conclusion
Digital printing is a game-changer in the textile industry, offering unmatched flexibility, speed, and sustainability. By adopting digital printing, textile manufacturers can stay ahead of market trends, reduce environmental impact, and deliver high-quality, customized products.
For comprehensive solutions in textile manufacturing and sourcing, visit locofast.com. Locofast offers a robust network of suppliers and manufacturers, providing high-quality textiles and reliable services to meet your business needs. Explore their website today to learn more about how Locofast can support your journey toward excellence in the textile industry.